Isn’t Higher Quality Supposed to Cost MORE?!
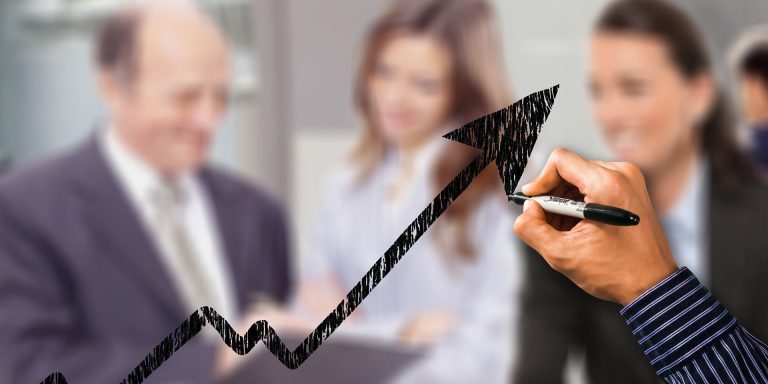
A couple of set-up questions. (1.) Do material cost reductions have greater impact on cost than production factors? (2.) Does higher quality cost more in production than a low process yield and the resultant higher rework hours?
The Director of Operations had set an expectation for his Business Unit Program Managers (or BUPMs) for a monthly report on cost reductions achieved, against a target he had set. The same Director had an expectation for an annual report on product quality improvement as measured by end-of-line acceptance test first-pass yield (FPY).
It always struck me as strange that the two Key Process Indicators had such different expectations – every month for cost, once a year for quality.
The natural behavior for the BUPMs that resulted from these expectations was a constant emphasis on product cost, negotiating lower material pricing, buying components in large quantities for better unit pricing, pressuring employees to work faster, and employing other tactics to hit the monthly cost reduction targets.
In contrast, the effort toward quality improvement was mostly limited to checking shop floor control system data at month-end to see if test FPY increased (hooray!) or decreased (aww…) from the prior month.
One enterprising BUPM took a different approach. Audrey’s business unit produced a mix of 21 unique products in a process consisting of manual and automated assembly and test operations.
Rather than trying to find ways of reducing supplier material pricing in a mostly futile effort to achieve her cost reduction targets, she focused her team on quality, and reducing the defect rate in the process.
Knowing that the cost of poor quality (COPQ) is real, tangible, and measurable, Audrey set out to improve her business unit’s production quality and thereby reduce the COPQ and answer the question:
Does higher quality cost more?
She created a Yield Improvement project involving her 6 process and test engineers plus 3 factory technicians, to address and correct the causes of low yield. Spoiler alert – it worked, and her business unit actually achieved their quality AND cost improvement targets consistently. Here in a nutshell is how Audrey’s team did it.
Failure Pareto Analysis
Instead of treating all products as equal, Audrey’s team disaggregated the test yields for the 21 products, to see clearly which ones had the highest failure rates. They created a Pareto chart of test failures for each product and focused on the highest-rate failures first.
Starting from the failure Pareto, they sought to determine the underlying defects for the highest failures. This activity actually consumed most of the daily effort for the Yield Improvement project, since most test failure reports don’t indicate the defect.
For example, the test report for a unit may say “Wi-Fi failed to connect.” Further analysis is needed to determine whether the fault was due to a component defect, interconnect defect, firmware error, access point dropout, or other product or process defect.
Defect Root Cause Analysis
Once an assignable defect was determined, the root cause(s) of the defect had to be identified. Here’s a little secret about testing and defects. Defects are detected by test operations, but they are created upstream in an assembly operation or a supplied component.
In order to improve test yield, it is necessary to put attention where the defects are created, not only where they are detected.
Working on the defects causing the highest-rate failures first, the team identified corrective actions to eliminate the causes of those defects. Ongoing process control ensured those root causes did not recur.
The Effect on Labor Cost
As defect causes were systematically reduced, Audrey noticed that labor hours began to go down for those products the team was focusing on. Delving deeper, she found that the reduction came about primarily from the reduced time spent analyzing failures, reworking, and retesting the products.
She realized that was a natural by-product of the team’s effort. For the highest-volume line, 45% of the monthly labor hours were consumed by the 12% of units that failed final test.
Over time, as test failure rates dropped from 12% to 8%, then further to 4%, the rework labor hours were reduced by one-third, and then by one-third again. At standard hourly rates for the plant, the cost reduction in Audrey’s business unit was over $250,000 in the first year.
Summing Up: Does Higher Quality Cost More? No!
Over the next two years, Audrey’s first-pass yields continued to increase to 99.5%, a defect rate of 0.5%. As product quality rose, product cost declined, and secondary effects such as reduced warranty cost and improved customer satisfaction became apparent. This brief story makes it sound simple; however, these results required deep understanding of product design, process capabilities, test strategies, statistics, and problem solving techniques.
Opportunity often comes disguised as hard work, but is usually worth the effort, as Audrey and her team and company will attest.
Dann Gustavson, PMP®, Lean Six-Sigma Black Belt, coaches Program Managers and their teams to achieve extraordinary results through high-impact program execution. Prepare, structure, and run successful programs in product engineering, manufacturing operations (including outsourcing), and cross-functional change initiatives.
Contact Dann@Lean6SigmaPM.com.